Seguindo o fluxo das fábricas de ração chegamos aos silos de dosagem de matéria prima. É nessa fase onde será composta a formulação da ração, cada matéria prima, deve ser dosada de acordo com o que está descrito na formulação.
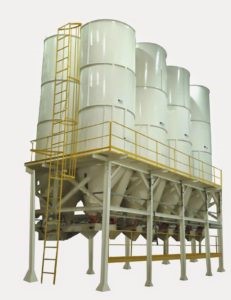
Nessa fase algumas pessoas ainda têm algumas dúvidas quanto à função desses silos, se eles são somente um silo de passagem, ou se pode ser armazenado outras matérias primas nesses mesmos silos.
Na verdade esses silos executam as duas funções, as matérias primas que são utilizadas em uma porcentagem pequena vão servir como silos de estocagem/passagem, como é o caso das farinhas de sangue e carne, farelo de soja, trigo entre outros e somente como um silo de passagem para o caso dos cereais de grande fluxo como no caso do milho e arroz.
A dúvida mais corriqueira que ouço sobre esse tema é a respeito da quantidade de silos de dosagem e a capacidade de armazenamento que a fábrica tem que ter.
Para um empreendedor que começa com uma fábrica de 2 a 4 ton/h, acredito que 6 silos é uma quantidade boa (para um projeto padrão), vale lembrar que alguns clientes já possuem contatos para a compra de outras matérias primas de baixo custo para fazer substituições, dessa forma essa pessoas costumam a trabalhar com 12 e até 14 silos de dosagem. Outro fator importante também é sobre o tipo de ração que ele estará produzindo, uma ração de combate, não tem a mesma quantidade de ingredientes que as rações Premium e Super Premium. Além de cereais e farinhas, essas rações costuma ter outros ingredientes que enriquecem a formulação e muitas vezes atuam de forma coadjuvante na saúde do animal. A parte de formulação e ingredientes será abordada de forma mais aprofundada nos próximos posts.
Quanto ao volume gosto de calcular de acordo com o fluxo da matéria prima de maior passagem.
Tomando como exemplo uma linha de 2ton/ h temos:
Uma fábrica com 6 silos de dosagem utilizará os seguintes ingredientes:
– Milho; Arroz; Farelo de Soja, Farinha de Carne; Farelo de Trigo e bandinha de Feijão.
Sendo a formulação com 35% de milho, o calculo é feito para que ele abasteça a linha por pelo menos 8 h de trabalho e dessa forma não seja necessário trabalhar com o moinho de grãos várias vezes por dia.
Voltando ao nosso cálculo de densidade e volume, temos:
Milho 0,70 ton/m³;
Produção: 2 ton/h * 8h = 16 ton/dia;
Consumo de milho: 16 ton/dia * 35% milho = 5.6 ton/dia de milho;
Tamanho dos Silos: 5,6 Ton/dia de milho / 0,7 ton/m³ = 8 m³;
Sendo um silo de 8m³ para armazenar 5,6ton de milho teremos um projeto de um silo com as seguintes dimensões:
Diâmetro: 2.230 mm;
Altura do Corpo: 2.000 mm;
Cone: 1.750 mm;
Ou seja, todos os seis silos terão esse mesmo tamanho.
Essa decisão deve ser bem analisada durante a fase de projeto, pois, ela irá afetar diretamente na altura em que seu prédio terá que ter, pois toda essa estrutura já estará dentro do seu barracão. Quanto maior a sua capacidade armazenamento, maior será o seu pé direito.
Hoje é possível trabalhar de diversas formas para fazer o melhor dimensionamento da planta, trabalhar com diâmetros maiores e menor altura no corpo do silo, ou até mesmo trabalhar com silos quadrados os chamados “Panelock”, por ser de fácil montagem e mais compacto, ocupam menor área na fábrica. Mesmo trabalhando com silos com diâmetros ou áreas maiores uma fábrica de ração no setor de moagem não tem menos do que 12m de altura devido a esses silos de dosagem.
A definição de onde cada matéria prima vai estar é muito importante para que não haja nenhum equívoco quando for acionado o programa para fazer o descarregamento e pesagem da matéria e para não ter problema com contaminação cruzada dentro desses silos.
Silos no qual estão armazenando as farinhas de carne ou vegetais necessitam de um dispositivo de vibração no cone, por serem de fácil compactação quando armazenadas por muito tempo, podem formar pontes dentro do silo e o produto não será dosado.
Na boca de cada silo sempre haverá uma comporta seja ela pneumática ou manual, ficando a cargo do cliente essa definição, caso o cliente não tenha uma opinião sobre o assunto será cotado para pele metade das comportas pneumáticas e a outra metade manual. As comportas pneumáticas são acionadas automaticamente de acordo com o programa da mesa de comando, e a comporta manual é necessário que um operador faça abertura e fechamento dela durante essa fase de pesagem, ou a mesma pode ficar meio aberta para que tenha um fluxo contínuo.
Abaixo das comportas teremos as roscas de dosagem essas são acionadas todas automaticamente de acordo com o peso da caçamba de dosagem, elas acionam e travam de acordo com o programa, elas são dimensionadas para cada linha de produção podendo ter diâmetros de 6”, 9”, 12” ou 14”.
A caçamba de pesagem é uma balança com células de carga na qual irá receber uma matéria prima por vez de acordo com o valor lançando na formulação do programa. Essa balança tem sistema de trava automática sendo que a batelada somente será liberada se o peso dela for igual ao peso cadastrado no programa. E esse peso pode estar incluso o peso dos micronutrientes (vitaminas e minerais) ou não.
Além dos macros ingredientes no qual acabamos de comentar temos também os micros ingredientes. Atualmente no cenário brasileiro temos 99% das fábricas de ração trabalhando com dosagem de micro ingrediente de forma manual, ou seja, todas elas têm uma sala de pesagem e um operador faz a pesagem dessa mescla de nutrientes em recipiente e depois ele é dosado manualmente ou na caçamba de pesagem ou na rosca de descarga da caçamba.
Para se automatizar essa linha hoje é necessária à compra dos mesmos silos no qual citamos para a parte de macro ingredientes, porém em uma escala menor de armazenamento, algo em torno de 250 a 500 Kg e todos eles tem que ser em aço inoxidável, por se tratar de material altamente corrosivo. Os demais componentes como comportas, roscas de dosagem e caçamba de pesagem também devem ser em aço inoxidável. É por esse motivo que as empresas ainda não migraram para esse sistema automatizado e por contarem com grandes empresas no Brasil hoje que entregam toda a mescla de micronutrientes em um único saco, sendo necessário o funcionário somente pesar a quantidade exata para cada batelada.
E comandando todos esses equipamentos temos uma mesa de comando, essa mesa tem que ter todas as formulações cadastradas no sistema, e a partir do comando do operador ela começa a descarregar as matérias primas na caçamba para compor toda a formulação.