O processo mais simples das fábricas de ração atualmente é a mistura, mas para que esse processo possa ter uma boa eficiência, é necessário ter uma moagem menor que 2,5 mm, ainda sim lembrando moagem com essa granulometria nos direcionará para um processo de peletização e moagem com granulometria entre 0,5 – 1,0mm processo de extrusão. A densidade determina a qualidade da mistura os melhores resultados são obtidos quando o peso específico dos ingredientes está na faixa de 0,5 e 0,6 kg/l. E o de aplicação de Líquidos não podem ser despejados abruptamente, e sim pulverizados, pelo o tempo correto e na dosagem correta, hoje no mercado já existem sistemas na qual se pode pesar a quantidade líquidos que será injetado dentro misturador de forma que não haja desperdício de matéria prima e de forma que o coeficiente de variação do produto esteja sempre ao redor de 5%.
Fatores construtivos dos equipamentos também são determinantes para que se tenha um alto rendimento no sistema de mistura:
1) Verificar a ausência de vazamentos nos misturadores, os locais mais comuns são nas comportas de descarregamento e nos eixos;
2) Deve ser de fácil limpeza e higienização, algumas empresa oferecem o misturados com portas de inspeção nas laterais para facilitar a limpeza, esses devem ser observados principalmente em misturadores onde ocorre a aplicação de líquidos, pois é muito fácil encontrar incrustação de matéria prima próxima ao local de aplicação e em misturadores de helicoides (ribonblender) que utilizam o sistema de cintas metálicas cruzadas dentro do corpo de mistura proporcionando cantos cegos e com isso acúmulo de produto.
3) Sistema de descarregamento do misturador, quanto maior a boca de descarregamento, mais rápido será a saída do produto e menor a possibilidade de que tenha contaminação cruzada entre as bateladas, a porcentagem de resíduos não pode ser maior que 0,2%.
4) O Coeficiente de Variação da Mistura (CV) deve ser menor ou igual a 5%, para indicar uma boa homogeneização das matérias primas.
5) Misturadores de paletas com um ou dois eixos apresentam uma versatilidade a mais que a de poder trabalhar com 30% de sua capacidade e ainda sim fornecer uma mistura com u CV em torno de 5%.
6) Devem ter boas respostas ao serem testados com Tracers**
A qualidade da mistura também pode ser avaliada através de um elemento traço, chamado indicador. Este pode ser especialmente adicionado à mistura, por exemplo, violeta de metila, micro-tracer, grafite, ou pode-se analisar um elemento da própria ração, como manganês ou cromo. A determinação da uniformidade da mistura pode também ser feita pelo Quantab, o qual mede o íon de cloreto presente na mistura. Atualmente, um dos maiores desafios é encontrar um método de avaliação da qualidade de mistura que não tenha restrições técnicas. O método de análise com violeta de metila não apresentava restrições técnicas. Mas, em função de riscos à saúde, a violeta de metila foi proibida na Europa. Os demais métodos apresentam restrições e podem ser questionados. Portanto, é preciso encontrar-se um método aceito pela comunidade científica e pelos usuários. Ter uma qualidade de mistura boa é fundamental, em especial para animais pequenos. Obter um coeficiente de variação de 5% com um determinado traçador (tracer), por exemplo, significa, na prática, que, em cada 10 gramas de ração, teremos todos os ingredientes que se misturam tão fácil ou mais facilmente que o tracer utilizado. Por isso, é tão importante usar o tracer adequado.
Fatores que afetam a uniformidade da ração
– Tempo impróprio de mistura:
Rotineiramente nos deparamos com a produção da mistura com o tempo inferior ao recomendado as vezes por desconhecimento ou as vezes por desleixo do operador. Os resultados confirmam o impacto negativo da produção de misturas com tempo inadequado, uma vez que pode onerar ate 1% o custo total da produção animal.
Cada misturador exige um tempo diferente para o processo ser eficiente e o tempo inadequado de mistura é a primeira razão para baixos resultados de uniformidade das dietas.
– Misturador sobrecarregado ou vazio:
Sobrecarregar o equipamento além de sua capacidade efetiva causa problemas como, por exemplo, cria pontos mortos de ingredientes que consequentemente não são incorporados uniformemente na ração. E o equipamento com a capacidade abaixo da recomendada impossibilita que o equipamento possa homogeneizar as partículas que ali se encontram.
A capacidade de carga dos equipamentos é calculada em m3 (metros cúbicos), isto porque a densidade especifica de cada ingrediente é variável ex: 0,7 m³ para o milho e 0,65 m³ para o farelo de soja, portanto o produtor deve levar em consideração a capacidade de carga de seu misturado para garantir a qualidade da mistura e maior durabilidade ao equipamento, já que o carregamento acima da capacidade ideal limita a vida útil do misturador.
– Desgaste, quebra e ajuste impróprio do equipamento:
Geralmente pouca atenção é dada a manutenção preventiva do equipamento, uma boa limpeza, lubrificação dos rolamentos e verificação da parte elétrica ajudam no processo de homogeneização das matérias primas. Os pesquisadores concluíram que em equipamentos com pouca ou nenhuma manutenção, o equipamento precisava de pelo menos 8 minutos para fornecer uma misturar com um coeficiente de variabilidade aceitável e em um misturador onde era realizada manutenções frequentes foram necessários de 4 a 6 minutos para homogeneizar a mesma matéria prima.
– Acúmulo de ingredientes nas maquinas:
Devido ao uso em quantidades significativas de gorduras, melaço e/ou aditivos líquidos pode ocorrer o acumulo de alimentos nas hélices, nas paredes e nas portas do misturador. Esse acúmulo pode ser diminuído fazendo a regulagem do bico de aplicação de líquidos, esse tem que formar uma névoa dentro do misturador para que o liquido possa agregar de forma igualitária as partículas que se encontram em homogeneização, para fazer essa névoa é necessária fazer o uso de ar comprimido junto com o bico spray.
– Erros de pesagem:
Erros de pesagem podem também criar problemas na uniformidade da ração. Atualmente as balanças usadas na grande maioria dos equipamentos possuem boa precisão, entretanto algumas medidas podem ser utilizadas para melhorar a eficiência das pesagens. Calibrar de tempos em tempos as células de carga da balança, reforçar o treinamento do seu operador que pesa os micro ingredientes, pois é nesse ponto na qual aparece os erros de pesagem. E se possível colocar um sistema de pesagem automático de micro ingredientes a principío é um investimento alto por se tratar de equipamentos todos em aço inoxidável porém isso fará com que a empresa economize alguns milhões na compra de premix prontos, no desperdício durante a pesagem e principalmente na falta de premix ou no excesso dessa matéria prima que esta sendo pesada incorretamente.
– Sequência imprópria dos ingredientes:
A sequência adequada de nutrientes pode afetar a uniformidade da dieta. Fazer pequenas mudanças na ordem dos ingredientes pode muitas vezes melhorar a uniformidade da ração. Por exemplo, a adição de melaço, gordura e/ou aditivos líquidos imediatamente depois da adição dos grãos pode fornecer uma melhor distribuição dentro do corpo do misturador, porém irá agregar maior acumulo de sujeira (grãos mais melaço) nas paredes e no eixo do misturador. A forma mais eficiente de se fazer a dosagem é do ingrediente com maior quantidade para o de menor quantidade para que os de menor % não se percam nos cantos do misturador e nem corram o risco de ficar no fundo, e só depois disso fazer a aplicação dos líquidos.
– Heterogeneidade da ração:
A segregação dentro da dieta pode muitas vezes acontecer quando um ou mais nutrientes se separam do resto da ração. A segregação pode ocorrer em diversas partes enquanto a ração estiver sendo misturada. Conforme já citado os principais problemas da segregação são: o tamanho da partícula, a forma, a densidade, a carga eletrostática, higroscopicidade, habilidade de fluxo dos ingredientes, como características que podem ter um impacto importante nos índices de uniformidade das dietas. Assim, o tamanho das partículas é considerado o fator mais importante. Por isso é importante revisar o sistema de moagem para ver se ele esta mandando a matéria prima sempre na mesma granulometria.
TIPOS DE MISTURADORES
– Vertical: São os mais baratos e comuns do mercado, esse misturador é alimentado na parte inferior dele e uma a matéria prima é jogada para a parte superior dele através de uma rosca sem fim. O produto acabado poder ser retirado pelas laterais dele através de comportas. Por ter baixa eficiência de homogeneização é necessário de 6 – 10 minutos para se completar uma batelada. Algumas empresas e consultores utilizam esse misturador antes do moinho de remoagem o do mistura alegando melhorar a homogeneidade do produto, eu particularmente não indico, pois ele não terá tempo de homogeneizar e ficar o tempo necessário irá atrasar o processo, o melhor mesmo é investir em um moinho horizontal com melhor eficiência.
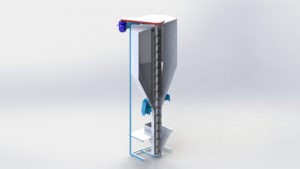
– Horizontal de Helicoides (Ribonblender): é o misturador mais comum nas fábricas de ração atualmente por ter um preço compatível com a sua função e eficiência. Possui tempo de mescla de 4 a 5 minutos. Possui somente um eixo, porém esse eixo possui duas cintas metálicas que se cruzam dentro do misturador, fazendo com que a matéria prima farelada dentro dele faça um movimento de vai e vem, ou seja, além de revirar, o produto vai ao centro e volta as paredes para fazer a homogeneização.
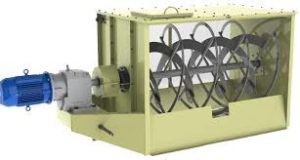
– Horizontal em forma de pera com pás (fast mix):
São a nova aposta do mercado atualmente fazendo com que o tempo da batida caia de 4 minutos para 1,5 minutos, além poder trabalhar com somente 30% da capacidade do volume do misturador. Possuem pás que reviram os ingredientes dentro deles e com isso alcançam melhor desempenho durante o processo. A grande sacada desse misturador é a descarga dele, pois ao invés de pequenas comportas pneumáticas que travam o processo produtivo, todo fundo desse misturador faz parte da comporta fazendo com ela abra totalmente liberando o produto com maior rapidez e com isso aumento o número de bateladas por hora em relação aos outros misturadores.
Existem outros tipos de misturadores com os de duplo eixo e os redondos com um eixo somente sendo esse eixo composto por pás ou helicoides, mas as principais empresas do ramo de ração animal oferecem esses três tipos de misturadores de acordo com o seu produto e a sua produção.
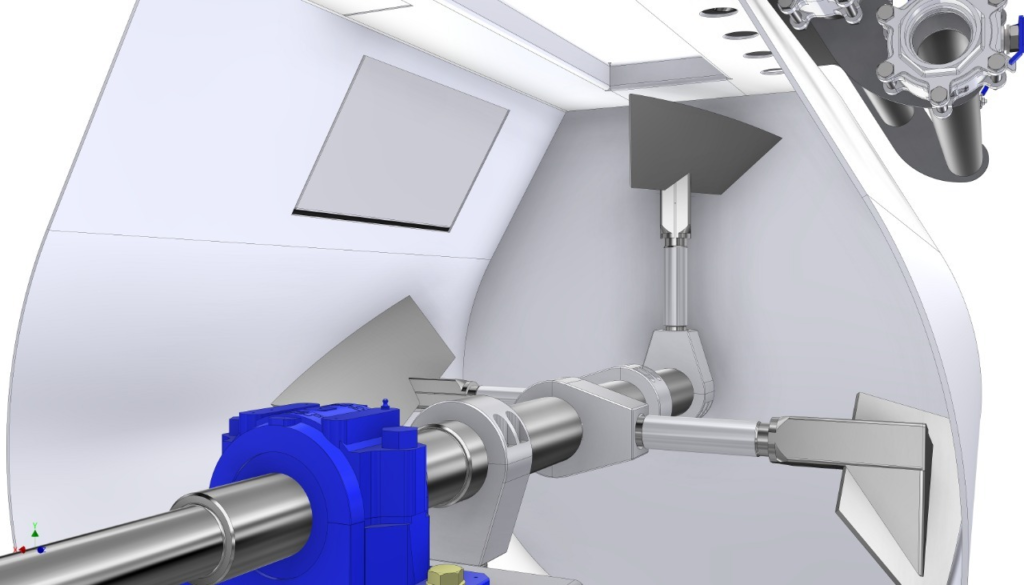
Partes que podem compor um misturador
– Peneira Rotativa: Em alguns projetos elas são colocadas para garantir que só irá entra no misturador partículas com a mesma granulometria.
– Silos Superior e Inferior: Esses silos são colocados nos projetos para que possam agilizar ainda mais o funcionamento da linha, pois enquanto o misturador trabalha, o silo superior está recebendo produto da remoagem e o silo inferior está dosando a matéria prima para os silos da extrusora.