Nesse ponto da produção é preciso fazer com que todas as matérias primas estejam na mesma granulometria. Para isso é utilizado o moinho de remoagem ou segunda moagem.
Os moinhos aqui são bem maiores do que os moinhos utilizados para quebrar os grãos no começo da produção.
Há pouco tempo atrás tanto peletização como extrusão trabalhavam respectivamente com remoagem em torno de 2 mm e 1 mm, hoje se sabe que quanto menor a partícula melhor o cozimento da matéria e consequentemente melhor a absorção dos nutrientes disponíveis na ração. Para não misturar os dois temas quando chegarmos à fase de processamento da mistura haverá um post para cada processo peletização e para extrusão.
Atualmente muitas empresas ainda trabalham com granulometrias maiores que 0,8 mm, mas a tendência do mercado é que todas elas cheguem a granulometrias que vão de 0,8 mm ou ainda menor.
Para peletização já se sabe que granulometrias em torno 500 a 700 micra (0,5 a 0,8mm), terá uma maior superfície de contato com o vapor fazendo com que esta tenha um melhor cozimento e como consequência melhore a taxa de absorção de nutrientes no momento da ingestão pelos animais. Rações peletizadas ainda possuem uma vantagem por apresentar ingredientes com baixa quantidade de gordura durante a moagem o que de certa forma auxilia na moagem.
Por outro lado na ração para Pet e Peixes, obrigatoriamente as empresas vem trabalhando com moagem não superior a 0,8mm para que com isso consigam uma ração mais homogênea com melhor cozimento e com melhor textura após a extrusão. Contudo já existem empresas que para ração pet já utilizam moagem 0,5 mm e 0,3 mm. Para ração de cães e gatos essas moagens são aplicadas para as rações Premium e super Premium para que elas consigam fazer o cozimento de toda a matéria prima durante a extrusão, é utilizado também para fazer nuggets por apresentar melhor textura e cozimento e ração com pequena granulometria.
Para a ração de peixe, vamos tratar primeiramente dos peixes de engorda essa pulverização da matéria prima é muito importante para que se possa fazer as rações inicias para alevinos, como estamos trabalhando com rações a partir de 1 mm é necessário que a moagem seja muito bem feita e que ela esteja com uma granulometria inferior a 0,8 mm que o tamanho na qual a matriz para essa ração deve ter, caso contrário a máquina não terá uma boa estabilidade e gerará diferentes níveis de pressão durante o processo gerando alguns estouros de produto na saída de matriz, má formatação da ração ou seja ela não terá um formato uniforme e o que de pior pode acontecer que o entupimento dos furos e até o travamento da máquina.
E ainda temos os peixes ornamentais e pássaros que utilizam esse mesmo tipo de moagem por serem rações de pequeno porte é necessário fazer uma boa pulverização da matéria prima. Hoje as empresas de ração seguem duas vertentes que são os moinhos de baixa rotação e os moinhos de alta rotação, segue o perfil de cada um deles:
– Moinho de Baixa Rotação: Esses moinhos trabalham com câmaras de moagem maior e possui menor pressão interna por possuir maior câmara de moagem e maior quantidade martelos, na qual ajudarão na moagem e trabalharão com rotação de aproximadamente 1760 RPM. A grande desvantagem desses moinhos é que para atingir a produção necessária utilizam motores mais potentes por ter menor velocidade e menor pressão interna.

– Moinho de Alta Rotação: Já os moinhos de alta rotação levam vantagem em praticamente todos os aspectos, possuem menor tamanho, otimizando o espaço da área onde será instalado, Esse moinho possuem menor largura da câmara de moagem o que aumenta a pressão dentro dessa câmara forçando a quebra das matérias primas, eles irão trabalhar com rotação de 3650 RPM, com menor número de martelos, ou seja, cada martelo bate o dobro de vezes sobre a matéria do que se estivesse trabalhando com o moinho de baixa. A classificação dessa matéria prima terá uma maior porcentagem concentrada em telas cuja granulometria é menor do a da tela onde foi feita a moagem o que é uma vantagem para o processo de cozimento. E a melhor parte é que esses moinhos tem menor gasto energético do que os moinhos de baixa. A diferença entre os motores pode ser de 50 – 100 HP a menos. Gerando uma boa economia no final do mês.

Partes que compões os moinhos
1)Alimentador Rotativo: A função dele é fazer uma dosagem dosada para dentro da câmara de moagem para que não haja acúmulo de produto dentro do moinho o que poderá favorecer o travamento e desarme elétrico. Boas empresas acoplam nesse sistema uma passagem com uma placa magnética, ela irá garantir a retenção de peças metálicas dentro do moinho e com isso prevenir a quebra de martelos e peneiras.
2) Câmara de Moagem: É nessa câmara onde estarão os martelos e a peneira, o sistema de montagem pode variar em cada empresa, mas normalmente se usa um rotor central com 4 eixos fixos na qual irá sustentar os martelos. Transpassando o fundo e as laterais têm as duas peneiras para a classificação da matéria prima. Na Câmara de moagem ainda possui um sistema na qual se controla a quantidade ar dentro da câmara, cada moinho possui a melhor regulagem para facilitar a entrada de ar.
c 3) Sistema de aspiração: Esse sistema é feito com sistema de filtros mangas e tem as seguintes funções:
a. Controle de resíduos em pó dissipadas no ambiente;
b. Aumenta a capacidade real do moinho;
c. Abaixa o consumo específico por tonelada;
d. Menos desgaste (martelos e Peneiras);
e. Para moagem grossa ele ajuda a reduzir a quantidade partículas finas.
Tanto a primeira quanto à segunda moagem apresentam esse sistema de aspiração visando atingir todos os objetivos listados acima.
Moinhos que não apresentam esses equipamentos irão gerar mais desgastes nas peças e maior consumo de energia para obterem um resultado esperado.
4) Caixa Plenum: Funciona como pulmão do produto moído e no fundo dela ainda existe uma rosca extratora que irá fazer a dosagem desse produto em algum elevador ou rosca. Ela tem a importante função de selar a entrada de ar através da caixa plenum, gerando um fluxo contracorrente o que poderia ser prejudicial para moagem abaixando o seu rendimento.
5) Freio Pneumático: Nesses moinhos ainda é importante lembrar a existência de um freio pneumático que agiliza a parada do mesmo. Quando uma tela se rompe e é necessário fazer uma parada rápida, esses freios são realmente importantes. Algumas empresas não adotam esse sistema de freios, mas possuem um sistema de troca das peneiras com o moinho em funcionamento, bastando para isso somente cortar a alimentação. Pessoalmente eu sou contra, pois em uma quebra de peneira o operador tem que visualizar o porquê da parada, se for um martelo o causador da quebra da peneira, em poucos minutos ele terá mais uma tela perdida.
Fatores que Influenciam a Moagem:
A moagem é influenciada principalmente pela matéria prima na qual se esta trabalhando, porém a velocidade do ar periférico, martelos e peneira são outros fatores ligados diretamente ao bom rendimento do moinho:
1) Matéria prima: a composição físico-química de cada matéria prima irá afetar diretamente na moagem dos ingredientes: quantidade de água, densidade, tipo da cadeia de carboidrato. Segue uma tabela abaixo para expressar essa dificuldade na moagem:
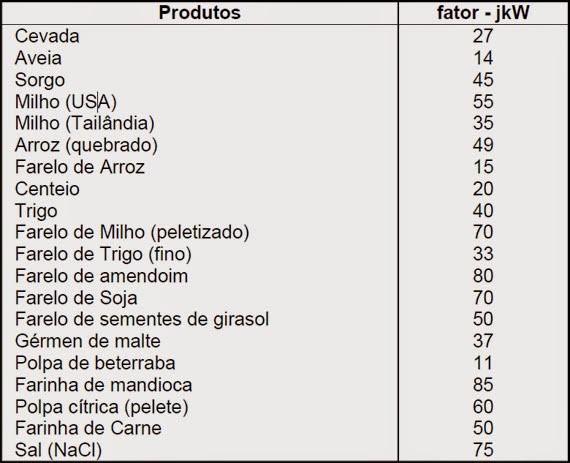
Essa classificação é referencial ao que já se foi testado e comprovado hoje nas fábricas de ração, sabemos que para que isso ocorra é necessário que a matéria prima esteja com uma umidade máxima de 12-13%. E a cada 1% acima do desse valor o consumo de energia aumenta em 7%.
A grande vantagem que se tem hoje é que como todas as matérias primas são moídas de forma conjunta a matéria prima na qual tem moagem mais fácil ajuda na moagem da matéria prima mais complicada além de manter a peneira sempre limpa.
2) Velocidade Periférica: Consiste num tipo de movimento de trajetória circular em que o módulo da velocidade é constante, ou seja, o os martelos sempre vão estar a 1760 ou 3600 RPM. Normalmente essa velocidade medida é de 90 m/s (325 Km/h) o que caracterizaria um moinho de baixa rotação, nesse caso a partícula encontra uma facilidade maior na saída da câmara de moagem quando essa já está no tamanho adequado. Quando essa velocidade é maior que 90 m/s que é o caso dos moinhos de alta rotação essa a quantidade ar gerado na câmara não deixa a particular sair e com isso ela é agredida mais vezes pelo martelo fazendo com que o tamanho seja menor do que aquele da peneira. O que explica o fato de moinhos de alta rotação tem uma classificação granulométrica com maior porcentagem em peneira inferiores a 800 mícrons.
3 3) Martelos: Em moinhos de baixa rotação se diz que quanto menor a quantidade de moinhos mais grossa a moagem, pois a matéria prima será menos agredida, e quanto maior a quantidade de matéria prima mais fina a moagem. Para baixa rotação isso é uma verdade e deve-se trabalhar dessa forma visando a melhor qualidade para os produtos. Contudo para moinhos de alta rotação essa quantidade de martelo é reduzida por causa do espaço dentro da câmara que também é menor, porém a velocidade compensa a falta de martelos, mas mesmo assim gerando uma moagem de alta qualidade. A manutenção desses martelos deve ser feito semanalmente ou quando se julgar necessário, pois o tipo de matéria prima influencia diretamente no desgaste dos martelos e também nas peneiras. Em um ano com pouca chuva gera grãos mais resistentes e abrasivos e quando esses passam pelo moinho provocam um desgaste maior do que grãos que receberam uma quantidade chuva maior. As variações dentro das faixas dependerão do produto que está sendo processado. Outra relação importante é obtida quando dividimos a potência do motor pelo número de martelos, que deverá estar o mais próximo possível dentro da relação: 1 CV para cada 1 a 2 martelos nos moinhos que operem em alta rotação e 1 CV para 2,3 a 3,1 martelos nos moinhos de baixa.

Martelos mais finos em torno de 3 mm tem uma eficiência melhor do que martelos com 9 mm de espessura esses mais finos tendem a empurrar a matéria prima contra a tela e com isso a granulometria fica mais grossa, ao contrário dos mais finos que reduzem a granulometria, dessa forma o consumo de energia é menor.
Visando o desgaste dos martelos algumas empresas têm investido em ligas mais fortes e até mesmo no endurecimento da área de contato com uma liga de tungstênio são medidas paliativas que encarece o produto e as vezes aumenta a vida útil do produto em 2 a três dias.
Martelos de boa qualidade tende a trabalha de 5 a 7 dias considerando gastar os dois lados e dependendo do volume de produção também.
Hoje no mercado existe uma infinidade fornecedores de martelos e a melhor forma de analisar cada um é experimentar cada um deles de acordo o preço que cada um oferecem. Mas antes de recorrer a terceiros consulte o fornecedor do equipamento.
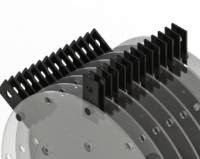
4) Peneira: A peneira esta relacionada diretamente com o tamanho do furo que se está utilizando, quanto maior o furo da peneira maior produção e menor o gasto energético. Segue abaixo a tabela de acordo com a furação.
RENDIMENTO DE MOINHOS – Mesh x KG x CV x Hora
· Peneira 0,5: 12,5 Kg/ cv / hora;
· Peneira 0,6: 15 Kg/ cv / hora;
· Peneira 0,7: 17,5 Kg/ cv / hora
· Peneira 0,8: 20 Kg/ cv / hora;
· Peneira 1,0: 30 Kg/ cv / hora;
· Peneira 2,0: 60 Kg/ cv / hora;
· Peneira 2,5: 62,5 Kg/ cv /hora;
· Peneira 3,0: 75 Kg/ cv / hora;
· Peneira 4,0: 100 Kg/ cv / hora;
· Peneira 5,0: 125 Kg/cv /hora;
Para saber se o seu moinho está produzindo a quantidade necessária para alimentar os equipamentos posteriores deve-se fazer os seguintes cálculos:
Ex: Para uma linha de 10 ton/h para extrusão – moagem 0,8mm
Um moinho com tela 0,8mm tem capacidade moer 20Kg/cv/hora:
Temos:
Produção = 10.000 Kg/h = 500 cv
Constante de moagem 20 Kg/cv
Para a linha de 10 Ton/h é necessário um moinho com motor de 500 cv para atender toda a produção.
5) Sistema de Alívio: O objetivo número um de um sistema de alívio de ar é o de incrementar a produtividade por kW hora, cortando custos operacionais e consequentemente aumentando os lucros. O objetivo número dois é manter a temperatura do produto com um acréscimo de no máximo 9º. C acima da temperatura ambiente. Isso ajuda a produtividade, elimina a condensação da massa de produto nos silos de processo, transportadores de rosca, elevadores e principalmente ajuda a não formação de pontes de farelo. O terceiro objetivo é manter a fábrica limpa, com menos pó, reduzindo assim o risco de explosão, abaixando as taxas de seguro e dando melhor apresentação à unidade fabril. O correto dimensionamento de um sistema de alívio de ar deve levar em conta além do modelo do moinho, a área perfurada de tela, o tamanho da partícula moída e o sistema utilizado para descarga do produto. Esses dados inter-relacionados determinarão a área da câmara de descarga, a vazão total do sistema e em consequência, a velocidade de arraste. Como parâmetros complementares, importantes para a qualidade e produtividade de um conjunto de moagem, podemos ainda destacar:
– O nível de umidade dos ingredientes que não devem exceder a 12,5 à 13%. Índices acima deste patamar reduzem fortemente a eficiência de moagem.
– Uma alimentação uniforme e constante, que utilize por igual toda a largura do rotor, o que é fator fundamental para utilização da capacidade total do sistema, e evitar o desgaste desuniforme dos martelos e telas (situação responsável pelo desbalanceamento do rotor)
– O dimensionamento correto da distância entre martelos e telas, da qual normalmente, a melhor eficiência é obtida com uma distância variável entre 8 a 10 mm.
– Manutenção preventiva. O efeito “corte” provocado pelos martelos e pelas telas tem sua maior intensidade quando os mesmos estão novos. Isto implica dizer que martelos e telas extremamente gastos são inimigos de capacidade, provocam aquecimento e baixam a relação Potencia x Capacidade.
Portanto telas e martelos devem ser mantidos em bom estado.
Esses, entre muitos outros, são detalhes que conjuntamente a uma instalação cuidadosa determinarão um bom sistema de moagem.
Ao final dessa análise temos que para a remoagem o melhor seria utilizar os moinhos de Alta Rotação por utilizar o motor menor e por conseguir uma granulometria menor, o que é altamente recomendável para os processos seguintes.