Nesta terceira parte do vídeo, vamos conversar sobre o tempo que passei em Santa Catarina e ainda sem saber muita coisa sobre extrusão, acabei pegando um desafio que para mim era muito maior do que aparentava ser.
Por não entender do comportamento das matérias primas dentro da máquina e o comportamento que elas iam ter para poder fazer diferentes produtos eu tive que aos poucos criar configurações que me resultasse em um produto na qual o cliente que possuia, porém feito com equipamentos muita mais capacitado para o serviço.
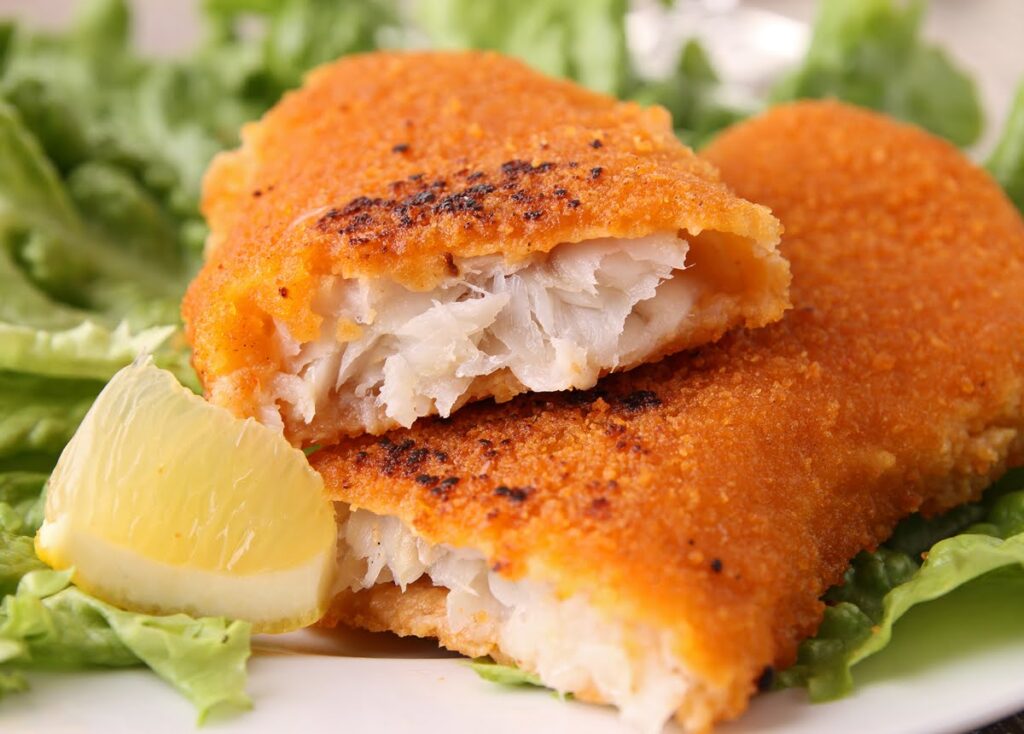
Foi nessa época que conheci o uso dos poligonais nos sistema de extrusão e seu efeito dentro dos equipamentos, outro ponto que comento nos vídeos e que foi fundamental para o andamento dos desenvolvimentos foi o uso de pré-condicionador para a acelerar o cozimento das matérias primas e assim conseguir produzir produtos com bom cozimento, aderência com cores mais vibrantes, talvez não são todas as pessoas que saibam mas as farinhas de empanamento recebem uma dose de corante para poder ter uma cor mais viva após a sua fritura, caso contrário ela ficaria com uma cor pálida.
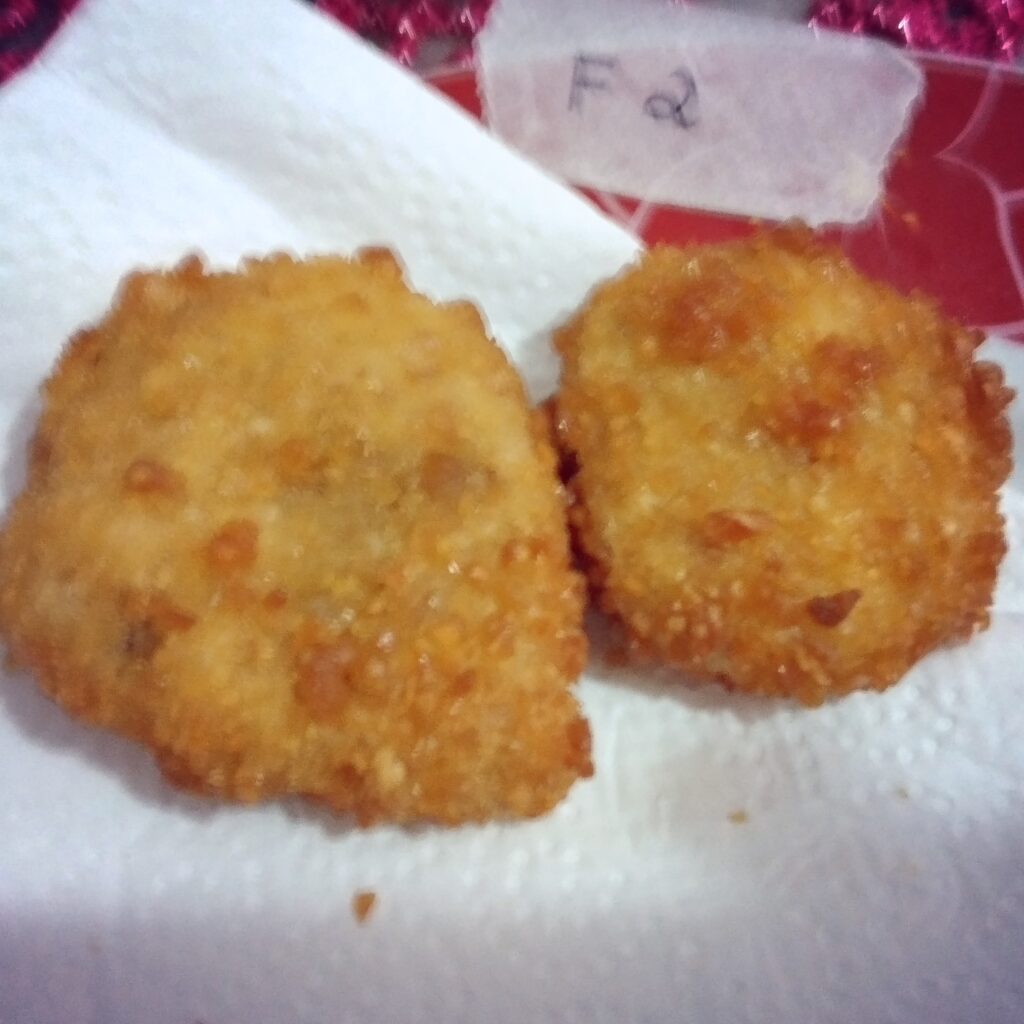
Mas o melhor dessa fase foi poder observar um equipamento de ponta como é o da Bühler e com isso procurar por melhores opções para ser fazer com nosso equipamento caseiro.
Como comentei anteriormente os primeiros equipamentos que vieram da China eram muito frágeis e quebravam com muita facilidade, só no período de teste tivemos as duas caixas de rolamento danificada e foi necessário refazer ela quase que por completo.
O dito popular, “O barato pode sair caro” é a sina dos empreendedores arrojados que buscam redução de custo melhores ofertas de investimento, mas como tudo tem um preço o nosso foi o da manutenção.
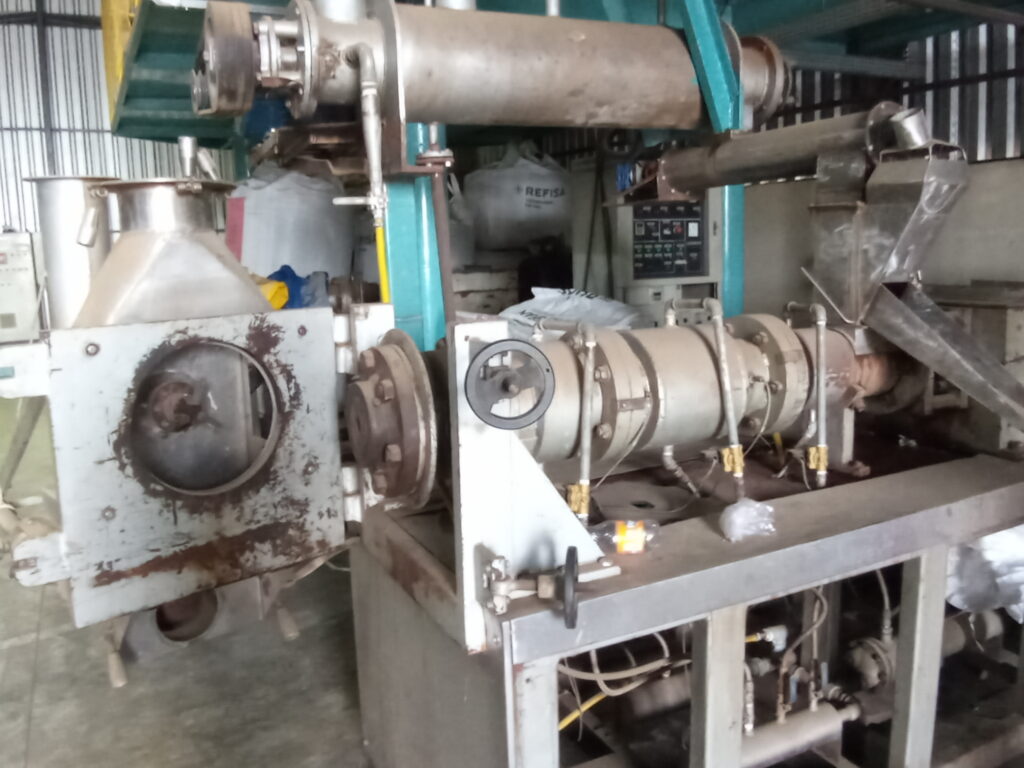
Após entender a forma de trabalho que o equipamento da Bühler tinha, pude fazer associações para os equipamentos chineses que rendeu uma melhora de performance e qualidade de produto, e com matérias primas complicadas como Creme de milho, amido de milho e farinha de mandioca, os equipamentos de que antes produziam 150 Kg/h cada, passou a produzir de 400 a 450 Kg com essas matérias primas pesadas para a extrusão e com motor de 150 HP cada, e quando produzíamos somente com milho triturado ela passou a produzir 600 Kg/h.
O ganho não foi só de produtividade, a qualidade dos produtos melhorou muito, e com isso abrimos novos clientes dentro e fora do Brasil.
Acredito que a história da Extrusão no Brasil teve uma única via de mão única até meados dos anos 2000. Desse ponto em diante o que antes era dominado somente pela Inbramaq, foi se diversificando e várias outras empresas nasceram e foram se especializando em produtos específicos, muitos migraram para ração e/ou snacks, que são os produtos mais fáceis de se obter por meio da extrusão, contudo outras empresas se aventuraram a fazer mais produtos e com isso a via que era de mão única se transformou em um grande malha rodoviária, onde é possível achar equipamentos de todos os jeitos, tamanhos, tipos e preços.
E essa foi mais uma parte da nossa evolução dentro da história da extrusão, espero que vocês tenham gostado e que possam compartilhar com mais pessoas que estejam interessadas no assunto. Abraço e até a próxima.